One of the things that many builders find daunting about the idea of manufacturing firearms completely from scratch, is manufacturing a rifled barrel. There are two tough nuts to crack with barrel making. The first is deep hole drilling, which is still called in industry “gun drilling,” because the technology of deep hole drilling, which today has many industrial applications, was initially developed for making gun barrels. Gun drilling will be dealt with separately; today, we’re going to talk about rifling a drilled (and, usually, reamed to precise size) barrel blank.
There are at least four processes used in industry to make barrels:
- Cut rifling: A cutting tool is drawn through the bore, using either a spiral guide or a system of gears. This method is used on most high-precision target barrels. It can be used for constant-twist or gain rifling, with an appropriate means of rotating the drawbar.
- Broached rifling: A carefully machined broach, a tool made of very hard material, is drawn through the bore in a single pass, stripping off material from the grooves of the rifling with teeth of gradually increasing depth. It cuts all lands and grooves at once, and produces a constant twist. The broach must be pulled, not pushed, and requires both a heavy, powerful, and specialized machine, and a specialized broach for each caliber, twist, etc. A barrel-rifling broach costs thousands of dollars (for comparison, a steel precision broach for doing the M16 mag well in 7075 forged aluminum is $10k for the tool alone).
- Button rifling: In this process, a carbide or other hard-material “button” is forced through the barrel.It cuts all groves at once (and smooths all lands at the same time), and can only produce constant-twist rifling.
- Cold hammer forging: the barrel is forged by a hammering machine, forcing an oversize bore to close in around a mandrel that is a mirror image of the intended rifling. Developed in Germany, it was first use on H&K weapons, then on TRW’s M14 contract. FN produces barrels this way, also. This forms the lands, grooves and usually the chamber also, all at once around a very expensive precision mandrel.
Of these, the only ones practically adaptable to the small-shop or home shop are cut and button rifling; you can’t hammer-forge or broach barrels on the cheap. It’s what MBAs call “capital-intensive.”
Home Rifle Cutting Lathe Attachment
This elegant lathe attachment, developed by an Australian gunsmith named Tony Small, uses a worm and spur gear to drive the rotating tool for cut rifling, while the barrel is held stationary through the chuck of the lathe. The handwheel drives a (nylon? Delrin?) idler wheel (the big wheel) which in turn drives Interchangeable gears, which are actually the speed-change gears from the lathe, to control the speed of rotation and thereby the rifling twist rate.
The drawbar attaches to the worm wheel and to the rifling cutter with precision tapered cross pins. Because his drawbar is 1/4″ diameter, he’s limited to calibers larger than that, ruling out all the .219-.224 calibers, but it would scarcely be rocket surgery to fabricate a drawbar for small calibers. All components except the speed-change gears were fabricated by Tony, including the worm and wheel. More information about this attachment is available on Tony’s website. That includes images of front and back of lathe chuck and worm wheel, an image of cutting the worm wheel (with a fly cutter in a milling attachment), and a custom-made short chuck he made to de facto extend his lathe’s travel compared to the factory chucks. There’s also a great deal more information in the comments to his YouTube video.
His lathe appears to be a Grizzly unit or something very similar. It is not a lathe that is out of hobbyist reach, even though he’s a professional.
The signal advantage of Tony’s machine is versatility. He can cut a wide variety of rifling pitches and calibers with a single machine. By making his own speed-change gears and perhaps another indexing plate (his present one accommodates up to 8-groove rifling) he could extend that, and make literally any barrel he can have a drilled blank for. This is well-suited for his custom-rifle business in Australia, where he handcrafts rifles for demanding shooters and hunters. (Do take the time to look around his site, and you’ll wish his information about his past work was more boastful, with more pictures of his classic, beautifully fitted and finished firearms. This rifling-machine post will still be here when you come back).
The disadvantages are that he has to make his own tools, and that it is unsuited for series production. It takes far longer to cut-rifle than to button- or broach-rifle a barrel. That is partly why cut rifling these days is the preferred technology of high-end barrel makers.
Hand Cutting Wooden Pattern Machine
This is a very primitive, 18th-Century machine (on 16th-Century principles), in a living-history exhibit. It was a live presentation, so it’s somewhat damaged by all the spectator conversation caught on the mic, but this shows the principles that were used on John Browning’s original sine-bar rifling machine (on display in his shop museum in Utah, it may have been his father Jonathan’s). Browning’s machine was all made of wood, not just the pattern. Of course, the greater rigidity of steel is superior.
This is a more “cottage industry” modern version, a home-fabricated all-metal version for short, i.e. pistol, barrels:
And here’s the crudest version, a failed attempt. This primitive machine is also made mostly of wood (warning: very slow video, very annoying music). It’s an experiment that falls well short of success, but points the way for better approaches.
Sine-Bar Cut Rifling Machines
Here is an American Precision Museum video of a 3D reconstruction of their 1853 Robbins & Lawrence Sine-Bar rifling machine. In this case, instead of a wooden pattern, an iron sine bar driving a rack and pinion imparts the twist:
The exact same principles were used in this sine-bar rifling machine, purportedly “Old Man Savages’s,” recently restored)… (see on YouTube to see the comments)
…and in the famous Pratt & Whitney rifling machines. This one is a circa 1900 one, probably a Nº. 3, but they were produced up to 1945. They are still around, but according to the video maker, most of the ones available these days are well beaten-up, and too expensive for the small shop anyway. There are two videos, and the comments in the original YouTubes here and here are worth reading, too. Part 1:
Part 2:
Home Button Rifling
Here is home-shop or small-shop rifling of a short barrel using a button and a 10-ton manual press to push it through. The manual press means the theoretical speed advantage of button rifling isn’t really achieved. It seems it would be straightforward to substitute a hydraulic press.
Buttons are widely available, direct from the manufacturers. Danjon Mfg. Corp (warning: crappy autoplay music), for instance, prides itself on selling to the one-man shop as well as to massive Remington. (Remington has used Danjon buttons for something like 50 years).
The advantages of cold-forming a barrel’s bore with button rifling include superior surface finish, surface, and ability to hold very precise dimensions. To get the best of these advantages, the bore must be drilled and then reamed to a very precise size to begin with. Disadvantages include an inability to cut really deep grooves; this process is limited to a depth of about 4 thousandths of an inch (.004″), max.
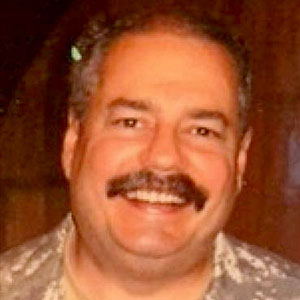
Kevin was a former Special Forces weapons man (MOS 18B, before the 18 series, 11B with Skill Qualification Indicator of S). His focus was on weapons: their history, effects and employment. He started WeaponsMan.com in 2011 and operated it until he passed away in 2017. His work is being preserved here at the request of his family.
13 thoughts on “Small- and Home-Shop Rifling Machines”
> danjon
That’s one of a handful of web sites I’ve encountered that seems to have been specifically crafted to REPEL any potential customers.
There’s not even an actual web page there, just a fixed-size Flash applet, yes, complete with noise. Not as bad as the blaring “racing engine” sounds at Comp Cams, or the blasting gunfire of a couple of firearms vendors… but… WHAT WERE THEY THINKING?
And it’s sad, because they’re actually a vendor of industrial tools that wants to sell to the little guy.
If you are interested in trying this may I suggest and old process called freshening. I used this to make several pistol barrels. An old mauser barrel was used, something the corrosive ammo had damaged. The rifling is cut deeper and the bore enlarged. I made 380 barrels for the old 32 autos,38 and 45 barrels for revolvers. The old barrels are heat treated and pressure tested so that isn’t required. A lot will tell you the twist is wrong,too fast. The only time the bullet acted strange was if I did something wrong. The twist never seemed to matter. The old guys did this to long rifle barrels and I only did it to short pistol barrels,but if you want to get you hand in,It’s a fairly cheap way to to get experience. Cutting the rifling and slowly boring it out is, I think, The hardest part anyway.
I still owe you some ISBN’s on books, and I’ll have to owe you some more information on rifling machines.
The Man on this topic was Harry M. Pope, of “H.M. Pope” barrels from 100 years ago. He rifled barrels on a lathe in a very similar manner 100 years ago. I believe his rifling lathe is now in the possession of a ‘smith in Vernal, UT.
In general, the most accurate barrels are single-point cut. Krieger and Bartlein make their barrels in this manner, and the proof is seen in target competitions all over the US (benchrest, F-class, etc). Button rifled barrels are plenty fine, and you can do button rifling with a broaching machine. You get a broach made with the twist and # of grooves you want, you put the pullrod through the drilled/reamed bore and you pull the button back through. It makes a hell of a bang as it comes out the end of the barrel.
In all of this, if you talk to barrel makers they will tell you what the hardest job is: reaming a straight hole. Deep hole drilling is not as easy as it looks, and before you can start talking of rifling a barrel, you need to drill the hole (undersized), then ream to straighten out imperfections, then you can start rifling.
When you’re all done, then there’s hand lapping, but that’s another story.
More later if you wish…
Your comments are very interesting. Thanks for posting them.
So much to learn.
Hognose- a fine point.
Buttoning does not “cut” the grooves as you wrote in the description. No material is removed. The button forms or literally squashes the grooves into the bore. Buttoning leaves stresses in the material that need to be relieved prior to turning the OD of your rifled blank.
Has anyone ever tried etching rifling? I’m caught up helping a cobber move house and repaint his former domicile, so I’ve got a plausible excuse for my laziness in not asking teh Interweb Oracle.
I’ve read of some people trying die-sinker EDM for cutting both the bore and the rifling at one go. It is rather slow, and the finish needs to be lapped smooth.
Howe’s “The Modern Gunsmith, Vol 2” has 5 chapters on barrels and barrel making. I have read the revised edition which is updated to 1941; there are others, both earlier and apparently later, but I know the 1941 edition is worthwhile This book has one chapter devoted to rifling barrels using minimalist methods entirely and is worth a read for anybody interested in the history of this technology.
Howe suggests that a milling machine is a better choice for rifling, BTW; a lathe is needed for other barrel making operations.
This book is out of print, but used copies are available. One can also get this from any large library.
Anyone interested in lower-tech approaches to metal working and manufacturing will get a lot out of this 2 volume set.
I dunno where my copy of Howe is; it’s a 1970s or 80s reprint. It has both volumes in one. I do remember those chapters (and indeed, that’s where I first learnt button-vs-broach-vs-cut. I just looked at my other gunsmithing books and Dunlap has a couple chapters, while Clyde Baker’s old book has barrel chapters by Townsend Whelen saying, basically, “it costs too much for the equipment to do rifling, so just buy surplus Springfield barrels.” That probably worked for Whelen, back then!
The sine wave rifling tool, are those expensive? I have seen a home rifling machine that used a piece of cut pipe and a hacksaw blade on YouTube. Looked rather crude, but the concept was interesting.
It would pretty easy to make a good low cost cutter using a CNC plasma with the pipe cutter attachment, and a half a day on the Bridgeport.
Two other methods come to mind (theoretical…..not tried and true….:
1) what about casting? Use clay or salt or ??? to get a copy of the internals of a current barrel. Perhaps you could cast via thermite
2) to refurbish an old barrel, why not electroplate the inside to add metal back to it (not only iron, but chrome could be used too)? Some additional reworking might be needed after re-metalling…..
Another website that may be worth looking over is http://www.hppublish.com. This site sells various DIY gunsmithing books by the late gunsmith Harold Hoffman.
The titles include how to make your own rifling buttons and rifling machines among other methods. I’m not personally or financially connected to this website and I have no idea how accurate and/or practical the information is.
I was previously aware of the website and it seemed relevant to this post so I’m passing it along. Hope it’s of interest to your readership.