A European website has a reprint of an excellent article by Vern Briggs of Ruger and Professor James Higley of Purdue. We’ve discussed the various ways of rifling barrels; we thought you’d appreciate Briggs’s and Higley’s deep dive into the process and technology of the most capital-intensive form of barrelmaking, cold hammer forging. (Actually, it could be hot hammer forging just as easily, as we’ll see at the end).
They begin with a history lesson:
To speed up production, German engineers came up with the hammer forging process to pound machine gun barrels to shape from the outside in. Interestingly, Remington took the opposite approach when it perfected button rifling a few years later by forcing the rifling from the inside out. These two differences play a large part in the behavior of the two barrel types which we’ll discuss shortly.
In the aftermath of World War II, forging expertise ended up in Austria with GFM (http://www.agfm.com/ in the USA), and they have become the leading hammer forging machine manufacturer with machines dating back to 1946. European gun manufacturers began using the technology shortly after the war while American manufacturers didn’t start until the 1960s.
As far as we know, the first use of hammer forging in the USA was by TRW on the US Rifle M14 contract. TRW was selected, in part, because it wasn’t a firearms manufacturer, but instead was a maker of machinery and aeronautical and automotive parts. Ordnance officers thought that TRW might be able to bring down costs and improve quality by applying automotive mass-production technology — and that’s exactly what they did with hammer-forged barrels.
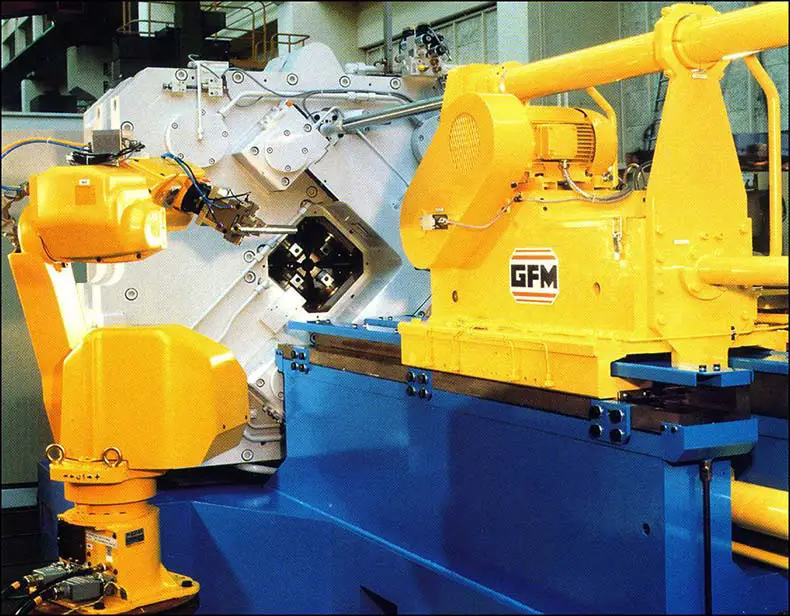
This is a big GFM rotary-forging machine with a robotic loader. GFM stands for Gesellschaft für Maschinenbau
Today, Sturm, Ruger & Company uses 6 GFM machines to make all their centerfire rifle, target rimfire, round handgun, and shotgun barrels. Remington has more GFM machines than Ruger, and other manufacturers have one or two machines each, some from other manufacturers. Hence, there are about 20 hammer forging machines actively producing barrels in the USA with none in the hands of small, custom barrel makers. The machines cost over a million dollars each, so it is no wonder only the largest firearms manufacturers have them.
Doing a little mental arithmetic, we can calculate that the sales of GFM machines to American gun makers only amounts to about $20 million over the past two decades or so, surely not enough to keep a large machinery manufacturer in business. In fact, barrel making is only a small part of GFM’s business; the automotive industry uses many of these machines, especially in Europe. American auto companies are starting to realize the benefits of hammer forging, and more and more forged car parts make their way onto the road everyday. While it won’t ever be as common as milling or turning, hammer forging has slowly become a common process in the manufacturing world.
The precision achievable with these machines is almost otherworldly.
While it seems like a rather crude process to beat the barrel down on the mandrel, the process actually requires quite a bit of finesse. Subtleties provide exceptional control of the bore and groove dimensions. For instance, the mandrel is tapered and can be moved in along the length of the barrel during forging. This provides two advantages. First, by precisely locating the mandrel in the bore, a specific bore size within 0.0001” can be obtained. Second, by adjusting the mandrel’s position during forging, the operator can create a tapered bore.
This was how the German war industries created the Gerlach taper-bore or squeeze-bore weapons during World War II. In essence, they used a tapering (but rifled!) barrel to squeeze down the driving bands on high velocity kinetic-energy rounds (with tungsten-carbide penetrators).
Here is how Daniel Defense makes an AR barrel, starting with steel rod, drilling a pilot hole, gundrilling the bore hole, then running it on the GFM machine, profiling it, chambering, etc.
One of the most interesting scenes (to us, at least) was the toolmaker using a surface grinder to reconfigure and restore the worn faces of hammers. The hammers last about 1,000 barrels before needing maintenance.
American GFM corporation links to a number of videos of these machines in operation. Here’s a sub-5-minute video of how a gigantic rotary forge machine takes a steel tube and forms it into a cannon or tank main gun barrel. It’s just like the Ruger or Daniel Defense process, except much larger — and the barrel preform is heated to roughly 2000ºF and maintained at that heat while being forged.
The Army designed and built its own machine, but it’s clearly a kissing cousin of the GFM hot-forge process.
The strengths of this process are speed and consistency. And the biggest obstacle to using this technology, of course, is the barrier to entry: such a machine is extremely expensive, even if you don’t need one big enough to work on 8″ guns.
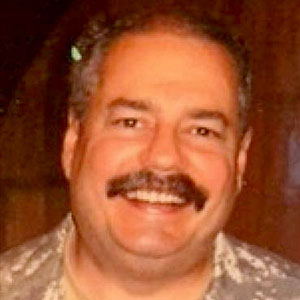
Kevin was a former Special Forces weapons man (MOS 18B, before the 18 series, 11B with Skill Qualification Indicator of S). His focus was on weapons: their history, effects and employment. He started WeaponsMan.com in 2011 and operated it until he passed away in 2017. His work is being preserved here at the request of his family.
18 thoughts on “How are Hammer Forged Barrels Made? And Why?”
FWIW: The linked article was originally published in the November 2005 issue of “Precision Shooting.” Professor Higley used to keep several articles on CHF barrels on his Purdue website. I can’t find the current link, but you can ferret out some of the articles via the Internet Archive.
https://web-beta.archive.org/web/*/http://technology.calumet.purdue.edu/met/higley/*
It is my understanding that the basic Cold Hammer Forged (CHF) rifling process originated at Gustav Appel Maschinenfabrik in Germany prior to the Second World War in order to form hypodermic needles. After the war began, the firm was chartered to apply the process to the manufacture of firearm barrels. Here are a few of the patents assigned to Gustav Appel Maschinenfabrik.
https://www.google.com/patents/DE768148C?cl=en
https://www.google.com/patents/DE768149C?cl=en
https://www.google.com/patents/DE1053287B?cl=en
Note that one of the listed inventors, Bruno Kralowetz, would go on to establish GFM GmbH in Austria in 1945. GFM GmbH ultimately became one of the largest suppliers of CHF machinery to the firearm industry.
Gerhard H. Appel attempted to bring CHF barrels to the American market in the 1950s. Alas, Appel was not equipped to deep drill or ream the barrel blanks prior to forging, and his source for the pre-drilled blanks had poor quality control. You can find Appel’s postwar US patents online under either his name or the assignee, Appel Process Ltd. The following link will take you to a review of Appel’s barrels published in the December 1957 edition of Guns Magazine.
http://www.gunsmagazine.com/1957issues/G1257.pdf#page=28
According to Roy Weatherby’s biography, the Mark V rifle was the first US rifle to be equipped with CHF barrels in 1959. At that time, the rifles were actually manufactured for Weatherby by J.P. Sauer in West Germany. Back in February 1971, American Rifleman ran the second of a three-part article by Jac Weller on the construction techniques used by US firearm manufacturers. Remington, Ruger, Weatherby, and Winchester were all cited as using CHF barrels for at least some calibers and models. In his 1977 book “American Rifle Design and Performance”, L.R. Wallack noted that Winchester was still producing CHF barrels, and their representatives had even claimed that they were the only major sporting arm manufacturer to chamber their barrels during the same CHF process. This technology even filtered down to legacy models like the Model 94.
Here is a better Internet Archive link for Professor Higley’s articles:
http://technology.calumet.purdue.edu/met/higley/index.htm
Thanks, this stuff is wonderful. I can’t understand why a university zeroes out a prominent professor’s pages when he goes emeritus or passes on. He’s part of your patrimony, Purdue!
I have several books by Wallack and keep meaning to add them to the Design Books page. In 1978 he had one book that basically combined his earlier books on “American … Design & Performance,” which were separate volumes on rifles, pistols & revolvers, and shotguns written over many years.
FYI: DTIC has several report on CHF. However, most will be found be searching “rotary forging.”
For instance, here is a report from TRW on prototype rotary swaged barrels for the M21 sniper rifle.
http://www.dtic.mil/dtic/tr/fulltext/u2/a008987.pdf
And here is another TRW report on rotary forging uber alloy barrels for the M134 and M219.
http://www.dtic.mil/dtic/tr/fulltext/u2/a019520.pdf
Another interesting post.
I worked for a company that took me through Cleveland, OH several times a year. I remember when I first showed up the locals were kinda like ‘welcome to Cleveland – booorrrring’ if you’re from CO. I quickly snapped back ” ARE YOU KIDDING? When I think of Cleveland, I think of the industrial might of the US!”
TRW is one of those Cleveland gems. There’s an American Rifleman article floating around on the web that shows TRW building those m-14’s.
My wife’s paternal grandfather was on Thompson’s board of directors after he retired from the AF. Think 4 star to Private Ind. And yes congress had questions. Think TRW mgmt. of ICBM dev pgms.
My grandfather retired from the AF and worked at TRW on the same programs. As a child I went with him and toured the Damascus, AR complex after an accident. Unfortunately, he wouldn’t let me go into the command bunker with the others touring the site.
John you need to read:
‘Command and Control: Nuclear Weapons, the Damascus Accident, and the Illusion of Safety’ by Eric Schlosser
You toured that site? WOW! Read that book. Breaks down minute by minute what went wrong in that silo. I was riveted, but I’m interested in WMD’s.
***This was how the German war industries created the Gerlach taper-bore or squeeze-bore weapons during World War II. In essence, they used a tapering (but rifled!) barrel to squeeze down the driving bands on high velocity kinetic-energy rounds (with tungsten-carbide penetrators).***
Clever, those Germans. I’ve always wondered about the how and why of the offset-from-centerline bore of the .276 Pedersen semiauto Luger-toggle action rifle design that lost out to John C. Garand’s more conventionally barrelled offerings, in both .276 and .30 M2.
I had often wondered just what CHF meant. Thanks for the basic introduction.
The M24 barrels are CHF if my memory serves correctly. The original barrels were from Mike Rock I think but I’d have to look up the history again.
Americans and Germans are using radial hammer forging to produce cheaper barrels which are functionally little different from those produced by other processes. French and Chinese are rotary hammer forging rifle and machine gun barrels from X1 CrNiMoAlTi 12 10 2 precipitation hardened stainless steel (closest American equivalent, 17-7 PH), an alloy which cannot be economically made into barrels by any process other than RHF. The X1 CrNiMoAlTi 12 10 2 barrels have far better high temperature performance and will run at red heat.
β-Si3N4 ceramic lined barrels are the future of military gun barrels, but PH stainless barrels would be a marked performance improvement as a technology bridge to that future.
I just put up (five hours late!) a post with more CHF detail… which may be wasted on you as I suspect you have the referenced documents already. The post does explain rotary and radial forging, I hope correctly, for the layman.
Could the X1 (etc) be made into barrels by cut rifling? Cut rifling is no longer considered economical in mass prod. due to the superior throughput of hammer forging and button rifling. One wonders if it can be automated to run faster. Limiting speed probably has to do with practical limitations on depth of cut and speed of cut, which in turn are probably more limited by chip removal than raw metallurgy — I guess.
Could the X1 (etc) be made into barrels by cut rifling?
Yes, but you would not achieve the full properties obtained by an RHF and age process. It is miserable stuff to machine, but it can be machined if you are willing to pay the price and be very patient. Its machineability is on a par with AISI Type 304 stainless steel without any machineability enhancement.
The massive, uniform cold work induced by RHF markedly improves the precipitation kinetics which strengthen X1 CrNiMoAlTi 12 10 2 steel. A good metallurgist can play around with the post RHF precipitation hardening age process to obtain remarkable properties. Think the Chinese are doing just this. They are very good metallurgists.
The alphabet soup European steel designations are actually the chemical symbols for the intentional alloying elements in order of their concentrations, followed by numbers which represent concentrations. In the case of ‘X’ prefixed stainless steels, the concentrations are in whole percentages for those alloying elements present at levels above 1%. So X1 CrNiMoAlTi 12 10 2 has 12% Cr, 10% Ni, 2% Mo, and sub 1% Al and Ti contents. The lower alloy, non ‘X’ prefixed, alloy steels also give you the chemical symbols for their alloying elements in order of their concentrations, but the following concentration numbers are factors which you have to memorize.
SMS makes more controllable hydraulic RF machines which allow many interesting permutations in rifle barrel manufacture:
https://www.sms-group.com/plants/all-plants/radial-forging-machines/
SMS also did not play footsie with the Warsaw Pact, back in the day. GFM markedly improved East Bloc aerospace metallurgy, something I will never forgive.
The founder of GFM does put one in mind of the version of Wernher von Braun from the Tom Lehrer song:
The GFM mechanical RHF machines are ferociously noisy and don’t lend themselves to effective sound enclosures. The hydraulic SMS RF machines purr like a kitten. You can talk in a normal voice without sign language right next to one running flat out.
That’s amazing. I mean, they’re hammering steel!